Critical Properties of Electric Vehicle Drivetrain Fluids
Battery-powered electric vehicles (BEV) are becoming more
prominent in the automotive industry. As the prevalence of these vehicles
increases, performance expectations are also increasing. OEMs and lubricant
manufacturers have realized that providing electric vehicle drivetrain fluids (EDFs) designed
to meet EV needs is critical to maintaining vehicle performance and meeting
customer expectations. The most important EDF properties for maintaining EV
performance include low viscosity, good gear protection, low foaming tendency,
excellent heat transfer, protection against corrosion and deposits, good compatibility
with polymeric materials, prevention of electrical discharge, and good
oxidation resistance [1,2].
Drivetrain Fluid Viscosity and EV Efficiency
Consumers are choosing electric vehicles because they perceive the promise of lower carbon emissions and reduced operation costs. Most electricity is produced by the combustion of fossil fuels at power plants, so vehicle efficiency is critically important to consumers trying to reduce their carbon footprint. Efficiency is also important to those trying to reduce the cost of driving their vehicles and to maximize the distance they can drive with current battery technology. BEVs have 3.4 times the efficiency of vehicles with internal combustion engines (ICEs); however, the drive system creates a greater portion of the total losses in a BEV [1]. These losses due to friction can be reduced by using lower-viscosity fluids. Traditional tests such as kinematic viscosity (ASTM D445), Brookfield viscosity (ASTM D2983), and high-temperature, high-shear viscosity (ASTM D4683) therefore continue to be critical for EV drivetrain fluids.
Gear Protection for EVs
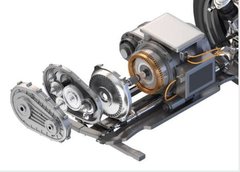
Traditionally, viscosity has been the main means of protecting gears. Higher-viscosity fluids provide a substantial protective layer between gear teeth that prevents contact and reduces wear. For EV drivetrains with low-viscosity lubricants to improve system efficiency, that layer is thinner and less effective. Another fluid-film problem comes from the nature of electric motors. Unlike in an ICE, the torque is at its maximum when the motor is starting from rest, and gears are exposed to high loads at low speeds [3]. High speeds are necessary to maintain an adequate protective fluid film. Therefore, additional means of gear protection are necessary. Gear protection is often provided by anti-wear (AW) or extreme pressure (EP) additives in the lubricant. The performance of these additives can be tested by several tribological tests that vary load and speed under lubricated conditions, such as the FZG Gear Test (ASTM D5182 or ISO 14635).
Reducing Foam from High-Speed EV Components
For any lubrication system, air in the fluid is a problem. It can interrupt the protective fluid films
and impair the fluid’s load- and heat-transfer properties. Foam is considered a
concern in EV fluids due to the high rotational speeds, propensity for fluid
shearing in the gears, and the lubrication and cooling techniques common
to EV drivetrain systems that promote fluid churning and splashing [1]. The tendency
of a fluid to foam and the time it takes for the foam to collapse are critical.
This is often controlled with silicone-based anti-foam additives. While they do
not exactly replicate conditions in an electric vehicle, the foam test (ASTM
D892 and ASTM D6082) and air-release test (ASTM D3427) may be used to assess
the effectiveness of anti-foam additives in EV drivetrain fluids.
Maximizing Heat Transfer with Fluid Properties
Lubricating fluids always play a role in transferring heat away
from the site of its generation. This role is more important for the electric drivetrain fluids than
other fluids. In addition to the heat generated by friction, there is a
significant amount of electrical heat generated in the motor. Many designs intentionally bring the
lubricant into direct contact with the motor windings and other electronic
components to cool them [4]. A number of fluid properties, such as density,
thermal conductivity, specific heat capacity, and viscosity, affect a fluid’s
heat transfer effectiveness [4]. For improved heat transfer, density, thermal
conductivity, and specific heat capacity should be increased while viscosity is
reduced. Each of the fluid properties can be determined with the appropriate
test: specific heat capacity (ASTM E1269, ASTM D7896), thermal conductivity (ASTM
D2717, ASTM D7896), density (ASTM D1298), and viscosity (ASTM D445).
Preventing Corrosion and Conductive Deposits
Reducing
corrosion and conductive deposits is important in electric drivetrain fluids. Any damage to electrical or structural
metallic components, such as circuitry or gears, is problematic [1,2,5]. Conductive deposits can create shorts that quickly
do severe damage to the motor windings [1,2]. Even non-conductive deposits
reduce the ability of the fluid to remove heat from components [4]. The
tendencies for corrosion and deposit formation often depend upon fluid
additives. Traditional corrosion tests ASTM D130 and ASTM D665 give a basic
assessment of a fluid’s ability to protect it from copper corrosion or rust. The
wire corrosion test (SAVLAB EV-WCT, ASTM designation in-process) and the
conductive deposit test (SAVLAB EV-CDT, ASTM designation in-process) give a better
indication of problems with copper corrosion or conductive deposits in EDFs because
they simulate conditions specific to EVs [1]. The Oxidation Stability Test (CEC
L-48) indicates the tendency for fouling by deposits, regardless of whether
they are conductive or not [4].
Assuring Fluid Compatibility with Polymeric Materials
Just as the metallic components of the drivetrain system need
protection, so do the polymeric components like structural plastics, seals, and
insulating materials. Contact with
fluids can cause swelling, changes in hardness, and changes in tensile strength
for polymers [2]. These changes in insulating materials can cause cracks,
chipping, thinning of coatings, or permeation of coatings. If the insulation is
sufficiently damaged, the possibility of damaging shorts occurs when electrical
components are spaced closely or conductive contaminants, such as corrosion and
wear byproducts, enter the fluid. One means of assessing material compatibility
is to measure tensile strength changes after exposure to the fluid. This
technique can be applied to hard plastics or to lower tensile-strength materials
as in elastomer compatibility tests (ASTM D4289, ASTM D7216, CEC L-112, ISO
1817).
Protection from Stray Currents and Damaging Electrical Discharge
Electrical discharges have a negative impact on corrosion, electrical component function, and gear and bearing wear [1]. Not only does the fluid need to avoid being electrically conductive, which would allow stray currents and could create safety hazards, it must avoid allowing static charge to build up to the point where a harmful discharge can take place [2]. This means the fluid’s electrical conductivity must be within the electrically dissipative range. There are several tests specifically for measuring the conductivity or resistivity of insulating transformer fluids. A related method, ASTM D2624, was developed for aviation and distillate fuels and gives similar information.
Maintaining EV Fluid Performance with Oxidation Resistance

Any effective electric drivetrain fluid will only be effective as long as it maintains its properties. The primary means for lubricant degradation in most applications is oxidation. Oxidation can be caused by exposure to oxidizing chemicals and elevated temperatures. Fluids in BEVs do not need to contend with the reactive combustion byproducts that ICE lubricants must withstand. However, the fluid is exposed to elevated temperatures when contacting motor components [2]. Furthermore, lubricants are exposed to other materials that could catalyze the oxidation process, such as copper. Finally, any electrical discharge creates localized high temperatures that can cause oxidation [1]. Oxidation stability tests such as CEC L-48 or direct measurements of oxidation products using FTIR after aging or service (ASTM D7214) can be used to determine a fluid’s resistance to oxidation.
[1] Canter, Neil. “Tribology and Lubrication for E-Mobility: Findings from the 2nd STLE Conference on Electric Vehicles.” STLE, Oct. 2023.
[2] McGuire, Nancy. “Test methods for evaluation of electric vehicle drivetrain fluids.” STLE. TLT Webinar October 2023. https://www.stle.org/files/TLTArchives/2023/10_October/Webinar.aspx, accessed Oct. 30, 2023.
[3] Van Rensselar, Jeanna. “The Tribology of Electric Vehicles” Bearing News. June 7, 2019. https://www.bearing-news.com/the-tribology-of-electric-vehicles-2/, accessed Nov. 3, 2023.
[4] Gahagan, Michael, “Managing Heat Through E-fluids.” A Virtual Conference On EV Engineering, Charged Electric Vehicles Magazine, Oct. 5, 2023. https://chargedevs.com/oct-2023-session/managing-heat-through-e-fluids/, accessed Oct. 30, 2023.
[5] TotalEnergies. “TotalEnergies last-generation EV Fluids validated under real-life conditions.” 27/06/2023 – NEWS. https://lubricants.totalenergies.com/news-press-releases/totalenergies-last-generation-ev-fluids-validated-under-real-life-conditions, accessed Nov. 3, 2023.